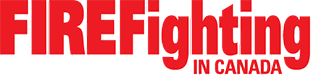
Equipment
Truck Checks: November 2009
About 10 years ago the diesel engine industry brought in some very interesting technology to reduce NOx levels (There are a number of Nitrogen oxide compounds that can be produced as a by-product of diesel engine exhaust so it’s easier to group them all together as NOxs rather than pointing them out separately, hence the x designation.)
November 6, 2009
By Don Henry
About 10 years ago the diesel engine industry brought in some very interesting technology to reduce NOx levels (There are a number of Nitrogen oxide compounds that can be produced as a by-product of diesel engine exhaust so it’s easier to group them all together as NOxs rather than pointing them out separately, hence the x designation.) Up to this point, engine manufacturers were concerned only with the black exhaust smoke that consumers could see coming from the exhaust stacks of trucks and buses. In an effort to reduce the black smoke –also called hydrocarbon particulate matter, or HCs – the manufacturers increased combustion temperatures and started using larger turbochargers with higher pressure boosts. This resulted in increased amounts of NOx gas coming out the exhaust pipe. While you can not see NOx gases directly, you can see their effects in ground-level ozone and in smog.
![]() |
|
Photo 1. A typical cooled EGR setup on a modern diesel engine; note the blue coolant hoses. Photo by Don Henry |
|
![]() |
|
Photo 2. Looking down on a typical DPF. The connection to the engine is on the right side of photo. Photo by Don Henry |
|
![]() |
|
Photo 3. Cutaway view of the inside of the DPF. Note the very small honeycombed passages. Photo by Don Henry |
|
![]() |
|
Photo 4. Note the white spark plug on a diesel engine, which is used to insure that the diesel fuel ignites during a regeneration cycle. Photo by Don Henry |
|
![]() |
|
Photo 5. DPF lamp on dash. | |
![]() |
|
Photo 6. Triangle amber warning light. |
|
![]() |
|
Photo 7. High exhaust temperature lamp.
|
One method used to reduce NOx involved injecting the diesel fuel later in the combustion cycle, a method known as retarded timing; this reduced the combustion cylinder temperatures and therefore also reduced the amount of NOx gasses being emitted. It also reduced combustion efficiencies, resulting in higher hydrocarbon emissions (black smoke) and less-than-acceptable engine performance. Advancing the injection timing gives the air and fuel more time to mix in the combustion chamber. This causes higher combustion temperatures, less un-burned fuel and reduced hydrocarbon emissions. Now, if this sounds too good to be true, you’re right. Advancing the timing also causes higher NOx levels. So, in cleaning up the black smoke we pumped out a gas that you can not directly see. It was a bit of a tug-o-war. Trying to reduce one problem increased the other.
The other gases commonly found in exhaust fumes are water (H20), which is harmless, and carbon dioxide (CO2), which is thought to contribute to global warming and climate change. The solution at the time was for manufacturers to add some of the already burned exhaust gases to the intake air of the engine. This is called exhaust gas recirculation, or EGR for short. This was not a new to the industry; it had been used in automotive gasoline engines since the 1970s. If you add inert gas to the combustion process you reduce the peak temperatures and this has the effect of reducing NOx production. It also has the effect of reducing engine performance. To offset this loss in performance it was necessary to increase the cylinder pressure. This was done by making increases in engine compression ratios. This caused stress on other engine components and therefore better engine oil was needed. I think you know how I feel about oil analysis; this is just another reason to get an oil analysis program. The EGR system also had other effects on engine systems. It would have had a very detrimental effect on engine performance if hot exhaust were added to the intake air of the engine.
It would be necessary to cool these exhaust gasses before they could be combined with the incoming intake air. Engine manufacturers used the engine coolant system to also cool the exhaust gasses before they were introduced to the engine cylinders. That’s why this system is often called a cooled EGR system.
Simply put, a portion of the hot exhaust is on one side of a stainless container while engine coolant is allowed into the other side of the device. This exhaust gas cooling added about another seven to 10 per cent heat rejection load to the already taxed fire apparatus cooling system.
In short, if you had a less-than-adequate cooling system maintenance program before, you were now about to get caught with your pants down. This is another good reason for coolant filters and a good coolant analysis program. While this technology was adequate to reduce the N0x emissions from the four grams per brake horsepower levels required in 1998 it would not be enough to meet the 1.20 g/bhp-hr requirement of 2007. The solution most manufacturers used is a combination of EGR and another method known as selective catalytic reduction, or SCR.
The catalytic device is often called a diesel particulate filter, or DPF. This is also called an after treatment device because it treats the exhaust after it has left the engine. It is placed after the engine in the exhaust pipe. Like all filters, it is possible to plug this filter, and this filter tends to plug faster if the engine does a lot of slow speed operations such as idling for long periods of time. Apparatus often idle for lengthy periods at accident scenes.
It is very important that only ultra-low sulfur diesel fuel is used in these units. If your fire department has a stock of diesel fuel that can be accessed during an emergency such as an electrical power outage, make sure it is ultra-low sulfur fuel. To clean out the filter, the manufacturers have developed a method of heating the DPF to a very high temperature. This burns any carbon off the catalytic bed. You could draw some parallels to the self-clean feature in your kitchen oven. There are different methods used by different manufacturers but they all involved spraying diesel fuel into the exhaust pipe between the engine and the DPF.
When the unit needs to go into this regeneration mode a DPF light will illuminated (solid) on the dash of the truck. This is called a Level 1 warning. The label on the visor above the dash will indicate that exhaust filter regeneration is required. You need only to drive on the highway at normal speed or conduct a parked regeneration to prevent future loss of engine power as the filter plugs. If the regeneration happens when driving it is called a passive regeneration; if it happens when parked and commanded then it’s called active regeneration. If you decide to ignore this warning the DPF lamp will flash indicating Level 2 soot loading. Your exhaust filter is now full; you will be prompted to pull the vehicle off the road and conduct a parked regeneration or you will have a loss of power. If you decided to not follow this warning you will get a Level 3 warning. This will continue, an audible alarm will sound and a triangle-shaped amber coloured warning lamp will light. In addition, an engine warning text will scroll across the dash on the liquid crystal display, but, most importantly, you will have reduced engine power. Even at this level it is still possible to conduct a parked regeneration and clean out the DPF. If you continue to ignore these warnings however, your engine will shut down, the stop-engine light will come on, the DPF light will go out and the text warning on the LCD will say “a serious engine problem has occurred”. There will be an expensive bill for a professional to remove and clean you DPF.
One other warning light I want to cover is the HEST lamp. HEST stands for high exhaust temperature lamp. It illuminates if temperatures above 400 C are reached inside the DPF. This is normal and can happen during either passive or active regeneration. Naturally these exhaust components and exhaust gases are very hot. Keep people and flammable materiel away from this exhaust. If you can’t do that, shut off the engine. I know you did not want to hear that but that’s the way it is.
An excellent presentation of this materiel was given at the Fire Rescue International in Dallas in August by Bob Neitzel of International Navistar. It was part of the two-day apparatus maintenance section workshop. If you would like a copy of this Powerpoint presentation, e-mail me at don.henry@lakelandcollege.ca and I will send it to you. It is a great driver training aid for your fire department.
Congratulations to the following technicians who have obtained their Master Fire Apparatus Technician rating with the EVTCC:
Myron Lachamn, Red Deer Emergency Services; , Alberta.
Joseph Limoges, City of Kelowna, B.C.;
Wesley Walker, Richmond Fire Rescue, B.C.
Don Henry teaches in the Automotive Services Technician and Heavy Equipment Technician programs at Lakeland College in Vermillion, Alta. He can be reached at don.henry@lakelandcollege.ca
Print this page