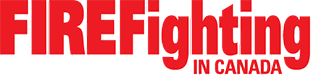
Features
Truck Tech: Lessons in preventative maintenance
March 15, 2021
By Chris Dennis
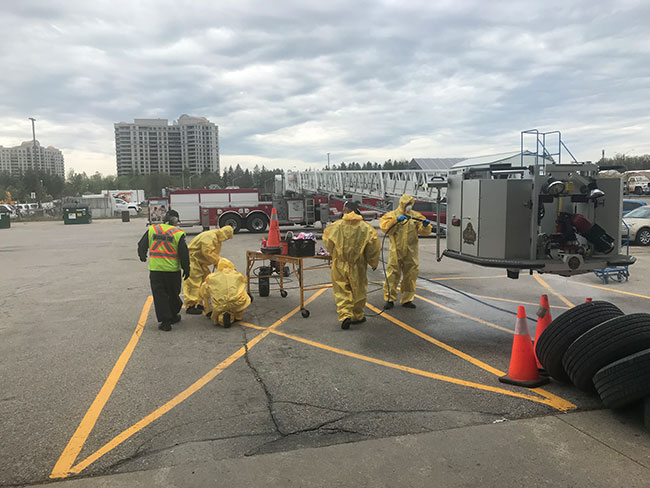
Hello all! With all the negativity and bad news we have had to bear already in 2021, let’s all hope that it does not last much past the cold months and we can enjoy family friends and fun in an up-close and personal fashion again instead of at a distance or via electronic solutions.
My article for this month is something I have written about before and need to circle back and go into some more detail. I have discussed preventative maintenance; how it helps to prevent early failures and also prepares us for future issues or impending failures. I always speak to subjects I have personally been involved with and this is definitely one of them.
We own a 100-foot custom steel mid-mount platform. The truck is a monster and so well suited for the job it performs. Like all trucks in any fleet, maintenance is key. But like all departments, we get busy. Sometimes the feeling of “it’s okay now I will get to it” went from one or two days day to a week or two months.
Your department may have specialized trucks like this one or maybe just one truck and you can’t afford to take it out of service for a small thing at this time, so you keep thinking, it will be ok we will get to it. Well, in our case something as simple as a dirty aerial ladder was more of a visual distraction than a function. Side note: Vaughan Fire Rescue suppression operations staff are our boots on the ground at the station level. Hopefully your department does daily truck checks. If it’s not a busy station you should be doing this biweekly. If so, well done. Whether full-time or volunteer, if it does not look or sound right, the odds are somebody needs to know what you know now. You can them discuss and determine a course of action.
A few weeks back a station, a captain called me to report a U-clamp that helps to support the water way was loose and hanging down. We did a face time and a video chat to get a feel for what was being described to me. This made the description process much easier to understand. With what I saw it was best to have it come in. When it got here the U clamp was an easy fix. One of our technicians noticed a cable sheave roller no longer running straight in line of load with cable. Further investigation proved the bushing the pin rides in was worn. It was bad enough we had to take the truck out of service. Once out of service, the sheave bushing and pin where destroyed. The pin had not been allowing grease to get to the bushing.
Let’s break down the complaint-cause-correction. The complaint: cable sheave not strait and beginning to rub through guide bracket. The cause: sheave pin not taking grease to the bushing. Destroyed pin, bushing, and sheave roller. The correction: inspect and replace all sheaves, sheave pins and bushings and grease fittings.
Why did this happen? We had performed a non-destructive ladder test (NDLT) in the spring of 2020 and it passed. The aerial was degreased and washed prior to the NDLT. Minor repairs where need and adjustments made at that time. It was back in service. We had seen the truck on and off throughout the balance of the year. Nothing serious. Then this: we discover that the grease is not getting through the pin.
Failure analysis proved a couple of things. These pins and grease fittings (certs) are the originals from 2009. Over years of servicing, the grease fittings have become plugged with road dirt and paint chips. The certs are all capped prior to factory painting but as time goes on and plastic cert covers fall off, the grease fitting is exposed to road dirt. As well, when greased, the paint chips that transfer from one grease fitting to another get pushed into the next grease fitting then pumped down into the pin. These findings over time allowed not just for one but two sheaves and bushings to be damaged. Inspection of all proved no other extensive failures but grease was not getting into places it should effectively. We contacted our parts dealer and ordered all new pins and sheaves. The pins came painted to match as well with new grease nipples. Only the grease fittings were painted over. As a technician, I knew painted grease fittings where going to be the beginning of the end of all these parts as well. We had to replace the painted fittings. Had we left them in, the new pins we would have been pushing paint into the grease fitting the first time we lubed the pin. Over time, the paint chips and grease would eventually block off or restrict the pin bushing from being lubricated and fail it again.
Whether it be a grease fitting on an aerial device or a grease fitting on anything else, be sure to clean the fitting first. If painted remove the paint. Be sure once greased the grease went where it was supposed to go. Over time check these greaseable parts to make sure they are functioning as designed.
The next item to address on this platform was dirt. I have included a picture of wash day. Spring is the time we do this, for the most part. The apparatus is always kept clean at station level, but the aerials are not that easy to wash. Therefore, we dedicate a time in the spring for every elevated device to come in and with a technician’s help degrease and re-lube the ladder. This is done with good grade degreaser as well as wash brushes. This has been what we have always done. Well this platform, in service since 2009, and missing a wash day, turned out to also be a contributing factor over time.
A licensed fire truck technician (EVT) has a solid working knowledge of how the aerial mechanics and components work. This is because this is what we are trained to do. Like a suppression firefighter sounds a floor in a burning building as they are trained to do. We are trained on specialty items in the mechanical world of vehicle repair. This also holds true for a general truck repair tech. Unless they were familiar with aerial devices and how the mechanics behind it work, they too would miss things. The dirt build up as well as de-icing agents had made their way into spots we had not encountered before. This assisted with the grim failure of pins and bushings. The entire aerial and platform were hand washed with special attention to mechanical items that in the past would stand the test of time. Lesson learned moving forward: We will be paying closer attention during spring clean-up. Washing an aerial by hand is long and tedious but at the end of the day the liability for failure is not an option. The OEM of all ladder makes has suggested maintenance intervals. We use this a guide to help us as create a solid history in the event it needs to be looked at. Take these lessons learned and share them with other fire departments and with your fire truck builder as well.
A partial digression — I have never been a Facebook guy. I recently became one as I had to know what my family was up to and how they were doing during these unprecedented times. I discovered fire apparatus repair groups that you can join and found it’s always interesting to get a different spin on repairs or troubleshooting or just find some plain entertainment. Well, that’s it for now.
Be safe. Be healthy. Be careful. Rubber side down my friends.
Chris Dennis is the chief mechanical officer for Vaughan Fire & Rescue Service in Ontario. He can be reached at Chris.Dennis@vaughan.ca.
Print this page
Advertisement
- Back to Basics: Ladder Dating — Getting on and off the ladder
- NFPA Impact: A fire chief’s role in sprinkler education