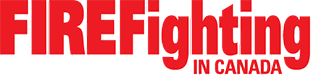
Equipment
Truck Tech: To refurb or not to refurb
Fire-service leaders today do a good job convincing council of the importance of upgrading the apparatus fleet. Municipality underwriter’s insurance companies are helping to lead the way. They are steering department recommendations towards becoming essential repairs and replacements in the eyes of council.
November 9, 2017
By Chris Dennis
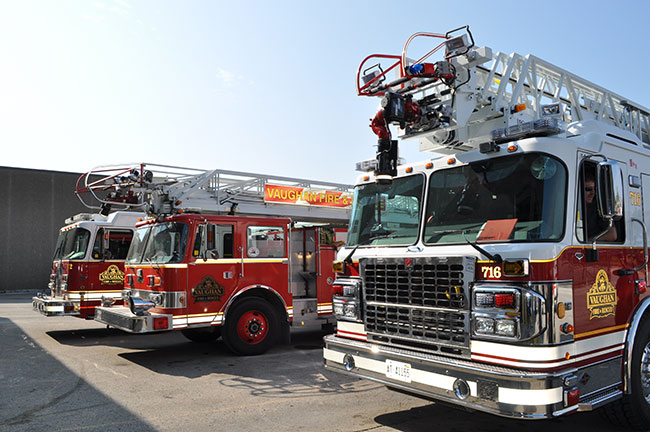
As far as I know, no one has come out and said this; it’s only my interpretation. I have been through two audits in my career and wrote an article on the experience for Fire Fighting in Canada in February 2014. It was a real eye-opener to see where our weak areas were, and where there is room for improvement. Even with a full mechanical repair division, Vaughan Fire and Rescue Service (VFRS) still needed to make some changes. Council and taxpayers will love you if the department qualifies for a lower insurance rate. However, with insurance companies driving rates up, the needs of the apparatus fleet can fall into the crosshairs.
The last article I wrote for Fire Fighting in Canada was on preventative maintenance. A good preventative maintenance program will help keep the apparatus on the road longer, while avoiding costly repairs or catastrophic failures.
It appears to me that every department across Canada, be it full-time, composite or volunteer, has a schedule for replacing trucks. Most are done via time cycles. For example, pumpers should be replaced every 12 years, aerial devices should be replaced every 15 years, and a new rescue vehicle should join the fleet every 10 years. Life spans can differ for every apparatus in every department. The full life expectancy of an emergency vehicle is 20 years, but the reality is, a lot of departments don’t have the funding to replace equipment. As a result, trucks are kept on the road much longer than recommended.
It’s all about money, and when it comes to fire trucks, nothing is under $100,000. Heck, a glorified pick-up truck from your local dealer can cost around $60,000. Some of the diesel-powered three-quarter and one-ton units can start at around $90,000, and that’s without a body. The sky is the limit for custom-built trucks.
In my shop at VFRS, we also do maintenance work for surrounding fire departments. Some of them are volunteer departments with minimal budgets. One department has two fire stations that house four custom fire trucks, and a number of utility and mini rescue trucks. The annual repair budget for the entire fleet is less than $ 15,000. The department is well outfitted, but the repair budget, in my eyes, is unrealistic. A brake job, one fire pump overhaul, and a tire change on one truck could be enough to gobble up the entire budget. This means the department should have budgeted for equipment refurbishment earlier in the truck’s life. Again, this is my personal opinion and not that of VFRS.
The odds are, these trucks will run for more than 15 years. When their time is up, nothing will go to reserve status or spare. It will just be junk, with very little trade-in or resale value. Departments are throwing thousands of dollars at a vehicle with no way of getting even a small percentage back at the end of its life span, because there was no regular maintenance. Typically, the trucks will be great for the one to three years. Around the three-year mark, we start to notice visible corrosion, wear and tear.
NFPA 1911 Standard for the Inspection, Maintenance, Testing and Retirement of In-Service Automotive Fire Apparatus and 1912 Standard for Fire Apparatus Refurbishing are the go-to books. Some departments may not have looked at this particular standard, especially if the department has only a couple of trucks. Reading this standard may help your department to make informed decisions.
So, to refurbish or not to refurbish? That is the question.
VFRS refurbished a 32-metre (105-foot) steel aerial four years ago. That truck was already 11-years-old and the repair costs were very high. However, because the maintenance had been accounted for, there were no surprises. The refurbishment went ahead because it would be three years before the department planned to bring in a replacement truck.
The new truck arrived this July and is currently in service. The previous truck, a 2002 custom aerial, has now gone to reserve. The fire chief looked at the expense of refurbishing the truck to remain safe and in service. But by keeping the truck as a spare, the department was able to avoid the high cost attached to continuing repairs. As for the new truck, we are already working on a timeline and budgeting for possible refurbishing and what it may cost to remain compliant with NFPA 1912 in the future. In the past, we have learned that the cost to refurb a unit that is over 20-years-old (besides a simple paint job) is not money well spent.
Drawing from NFPA 1912, here are a few common refurbishing questions fire chiefs should ask themselves before making decisions. Below is my advice for chiefs questioning whether to refurbish a vehicle or not.
Q What is the overall condition of the rig? Was there a significant repair done that may happen again? Overall, should you spend money on an apparatus that will continue to give your department little return?
A There will not be a large return for the money invested in an old or badly damaged vehicle. Keep good financial records of department spending for each truck. Look at the condition of the truck and the circumstances of your department to make calculated decisions based on both safety and taxpayer dollars.
Q Does the rig meet the current needs of the municipality or city? Are the functions are obsolete? Are the parts needed to fix it still available? Again, is it cost effective?
A Do not invest money into something that will come back to haunt your department with one repair after another. If you need a second opinion, contact a fire truck mechanic to give you his or her advice. Consider what your community needs and whether or not this truck can provide it. Safety is No.1. For example, imagine your community had only a few multi-story buildings or subdivisions with lots of undeveloped land 15 years ago; now a multi-story apartment complex is being built as well as larger subdivisions. The aerial device or pumper you currently have has a 5000 LPM fire pump, which could have handled anything the department threw at it 15 years ago. But now the community has different needs. Replacing the fire pump for a bigger one to meet multiple hose line needs is not cost effective. The multi-year strategic plan could help departments determine future truck purchases.
Q Once you have refurbished the truck, will it continue to be safe? Could it possibly meet the capabilities of a newer fire apparatus?
A It is possible that the refurbished truck will remain safe, and even match the abilities of a newer apparatus. However, there are a few key points departments should keep in mind when refurbishing a truck. For example, fire departments cannot change the gross vehicle weight when rebuilding the truck. If your truck needs to carry more water because the township or city got bigger, you can’t install a bigger on-board water tank, foam tank, or add on a large amount of extra equipment. A change in total vehicle weight changes the way a truck handles. The chassis may not have been designed to carry the amount of weight the city now requires. If you have an open-rear crew cab design truck and are looking to enclose this area, remember to be compliant to the standards. The enclosure may be enough to put the truck overweight, and make the vehicle unsafe.
Q If a truck could be refurbished regularly, will it be virtually major repair free? What happens if there is a major issue? How much longer will the parts last if a major break down occurred?
A Trucks are machines and mechanical components can fail. Like a light bulb, your truck may work one second and burn out by the next time it is needed. What I mean by this is that fire service leadership should prepare for failure, because all trucks will break over time. Ask other departments of your size what common failures are affecting their trucks. Can you apply this information to your fleet? Find out who does their maintenance work and recertification. During the initial truck build, be sure to add the length of time the manufacturer has been in business in your RFP or bid for tender. Find out which departments have the trucks and ask what they do for parts and service assistance, especially on trucks over 15-years-old. Best practice is if the repair cost is more than the truck is worth or repairs over time have added up to the same initial cost, then it’s not a good choice to move forward with repairs or refurbishing.
Q If a truck has a good trade-in or sale value today, will the rig still have value in a few years? Does the refurbishment cost compare to (or outweigh) the cost to get a new or used rig?
A Resale value is all about transparency. The taxpayer wants the best return for their dollar. Most fire apparatus over 12 to 15 years-old have little trade-in value. To get the most out of new or used vehicles, create a maintenance plan the day it is delivered. At the beginning of a truck’s life departments should also take into consideration the middle and end of its life cycle. To a certain extent, chiefs can use regular maintenance to set a truck’s life cycle to fit the department’s strategic long-term plan.
Whatever you decide, keep in mind that firefighter safety is paramount. Crews should have access to a reliable rig so they can perform the tasks they were trained to do. An unreliable fire truck that could potentially break down could jeopardize the safety of all, while failing to fulfill the needs of the department.
To quote NFPA 1911 “An old, worn out, or poorly maintained fire apparatus has no role in providing emergency services to a community.”
Thanks friends. Be safe and remember: rubber side down.
Chris Dennis is the chief mechanical officer for Vaughan Fire & Rescue Service in Ontario. He can be reached at Chris.Dennis@vaughan.ca
Print this page
Advertisement
- Specific specs: Departments consider community needs when buying trucks
- Trainer’s Corner: All firefighters should understand wildland terms